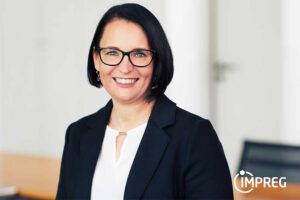
10-year employee anniversary
Katrin Letzgus-Danhach, our Business & Sales Manager, celebrates her 10 year anniversary.
Learn more about IMPREG and our new paths
To get something done, you have to tread new paths. This has always applied to IMPREG since the company’s birth in 1999. We recognised early on that trenchless pipe rehabilitation using CIPP liners is the technology of the future.
We are continuing into the future along this path. Our CIPP liner systems are developed using innovative high-tech processes, and set new standards. They can be used to master even highly complex tasks.
Our success proves us right. IMPREG CIPP liner systems for UV curing are used all over the world. We are reliable solution partners at all times, and commit ourselves to the highest future-proofed quality and to environmentally conscious conduct.
Katrin Letzgus-Danhach, our Business & Sales Manager, celebrates her 10 year anniversary.
We are very proud of two loyal employees and congratulate them on 20 years of service with Team IMPREG!
On Friday, 3 February 2023 IMPREG’s 8th International Operator’s Meeting ended.
Melis Abdulahovic successfully completed his IHK (International Handelskammer – International Chamber of Commerce) further education to acquire an IHK certificate
Robert Papp – the end of a cherished era Robert Papp, IMPREG founder and long-time COO of the IMPREG Group,
Lanes Group, specialists in sewer maintenance in the UK, has installed its largest UV liner.
As an internationally active company, our values in interacting with our employees, customers, and partners are our best resource for reaching our company goals.
Imagine that you can work in a young, motivated team within an internationally strong, growing company. Start your career now.
The importance of trenchless sewer rehabilitation
© 2024 IMPREG GmbH